Industrial automation is the use of technologies to perform tasks that were previously considered repetitive, automatically and with minimal human intervention.
Technologies for such processes are becoming increasingly common in factories as they seek to move away from manual processes.
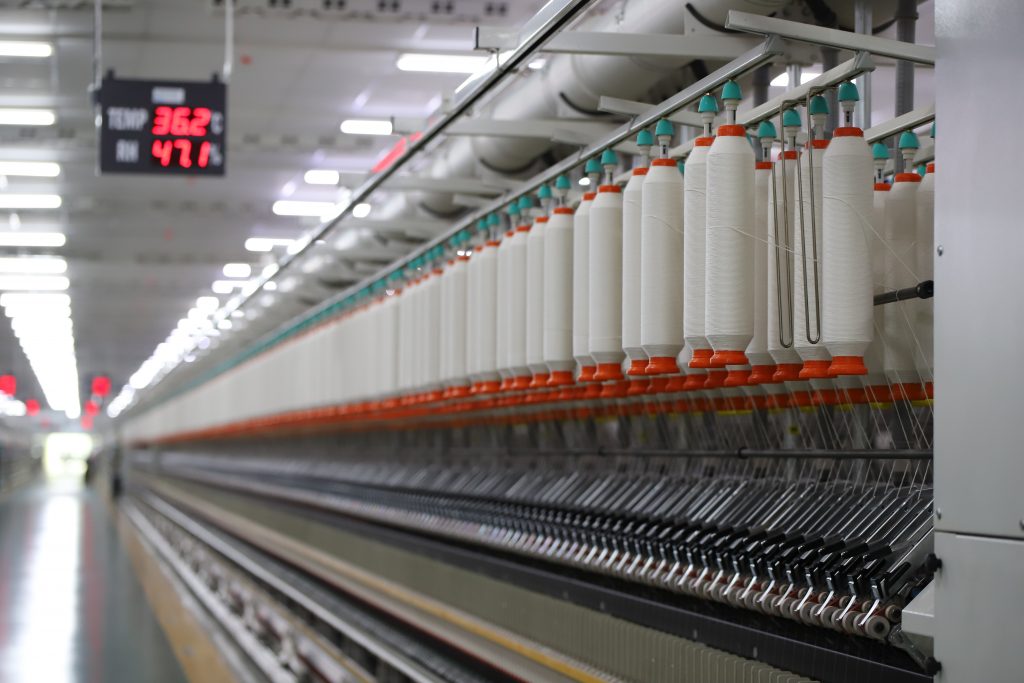
Read more about Industrial Automation
What are the benefits of applying Industrial Automation to a company?
Among the benefits that industrial automation brings to companies are, for example:
- Increased production of different products.
- More homogeneous and quality manufacturing.
- Reduced margin of error in production as it is a computerised process.
- Constant production of products and therefore without interruptions.
- Reduction in manufacturing times and therefore also in material and labour costs.
- Safer processes for people through control.
Industrial automation is a key element in key element in
the digital development of the company.
Sectors
Within the industrial sectors where an industrial automation project can be executed, we highlight:
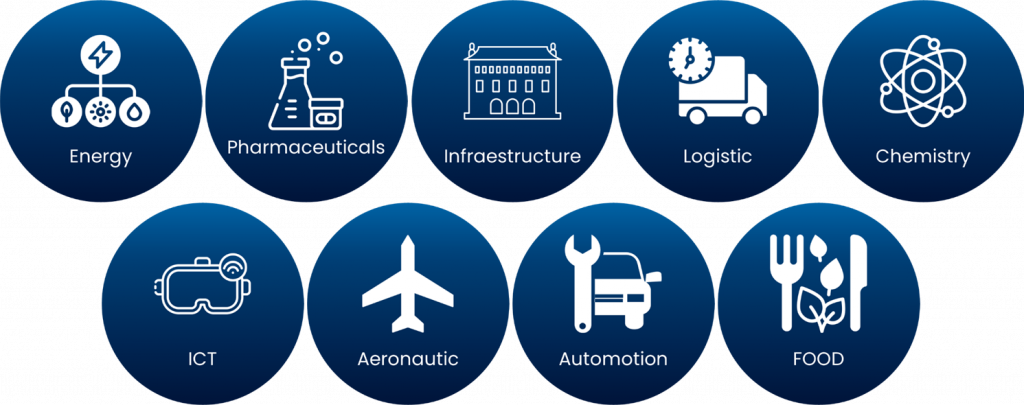
Project 1.
Automation of robotic line for sheet metal stamping.
AUTOMOTIVE SECTOR
Programming of safety and manoeuvre of a line of presses, managing permissions between press-robot and interaction with the user. Integration of the vision system and other external elements such as parts washer and conveyor belts. This is a complex installation where all the interactions between user and machine are managed in order to have a line that is safe for people and efficient from the point of view of productivity.
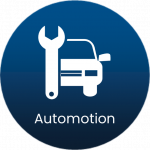
Project 2.
Implementation of a robotic cell for palletising boxes in a logistics company.
LOGISTICS SECTOR
Displacement of technicians all over the world for the start-up of the palletising cell. The system consists of a code reader, communication with the company’s central system, case traffic management and communication with the palletising robot. The system has:
- Safety by means of emergency buttons and photoelectric sensors.
- AS-Y communication and configuration of roller conveyors via Ethernet/IP.
- Realisation of stress pot for validation with the end customer.
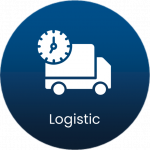
Project 3.
Programming and commissioning of two automated cells for the packing of food and frozen products.
FOOD SECTOR
Preparation of the programme in the offices and the technicians’ travel to the customer’s premises for the start-up of the packing cells. The system consists of.
- Conveyor belts for receiving empty crates and the packaged product
- Pick & Place shaft system to fill the boxes with the received product. The Pick & Place system includes different models of headers and tarpaulins to adjust to different types of product, and allows to fit in different floors and columns at high speed. It also allows case packing by turning the Pick &Place.
- Case erector and case sealer
- Weighing to control the received product and the filled case.
- Communication with the company’s central system and the upstream packer and downstream palletiser.
- Case traffic management
- Safety programme for the different elements
- Profinet, Ethernet/IP communications
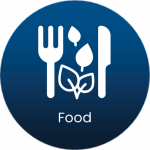
Did you like this article?
Receive new articles about technology and industry trends, and Industry 4.0 in your email weekly.
Subscribe to our newsletter
If you would like more information or have questions or ideas you would like to share with Innova IT: send us a message to comercial@innovait.cat or fill out the form below and we will get back to you as soon as possible.
For something more specific and concrete, make an appointment and visit us at our premises.
Industrial automation in 2023 - Innova IT
[…] Take a look at other automation projects we have carried out […]